Exploring Advanced Equipment and Techniques for Accurate Welding Inspection
In the realm of welding examination, the quest of accuracy and dependability is extremely important, spurring the growth of advanced devices and methodologies. Technologies such as phased variety ultrasonic screening and digital radiography are changing defect detection, providing unparalleled accuracy in defining welding flaws. In addition, laser scanning advancements and automatic examination systems, outfitted with expert system, are redefining the landscape by decreasing human mistake and enhancing security steps. As these innovative methods proceed to evolve, they guarantee not just to transform evaluation practices however additionally to increase appealing concerns concerning the future of quality control in commercial applications.
Ultrasonic Testing Innovations
Ultrasonic screening innovations regularly represent the center of developments in welding assessment innovations. These developments have dramatically enhanced the capacity to detect and assess interruptions within welded structures, ensuring enhanced honesty and safety - Welding Inspection Madison. Ultrasonic screening employs high-frequency audio waves to pass through products, providing detailed details concerning internal functions without causing damages. The most current advancements in this field have concentrated on increasing precision, speed, and the capacity to interpret complex information.
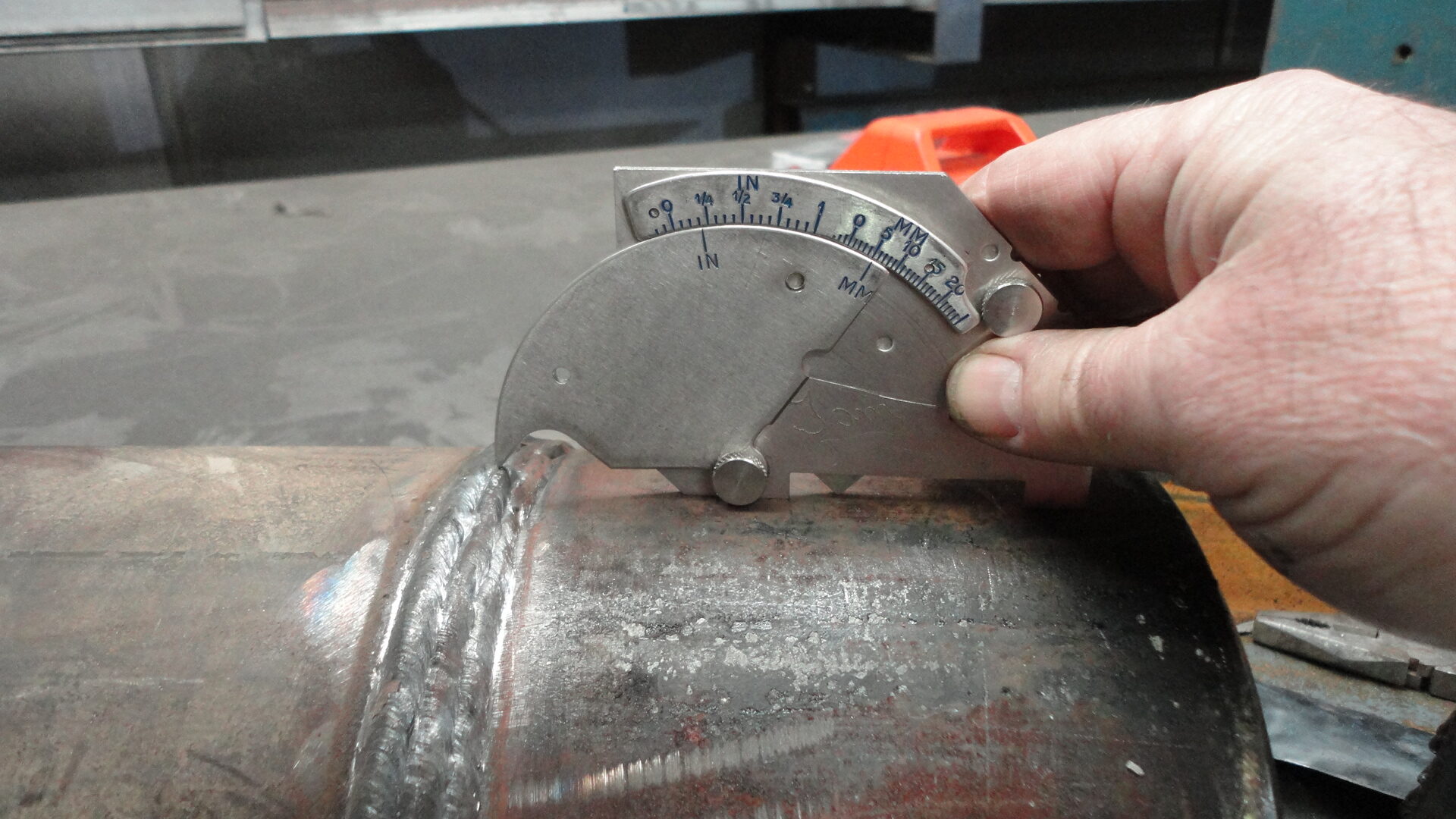
In addition, innovations in software application formulas for information analysis have actually enhanced the accuracy of problem detection and sizing. Automated ultrasonic screening systems currently use high-resolution imaging, enabling in-depth assessments of weld top quality. These systems are often incorporated with advanced visualization devices, which assist in the interpretation of results.
Radiographic Evaluation Strategies
While ultrasonic testing innovations have set a high standard in non-destructive assessment, radiographic inspection techniques remain to play an indispensable function in welding inspection by supplying distinct understandings into product stability. Radiographic testing (RT) employs making use of X-rays or gamma rays to pass through materials, creating a radiograph that aesthetically stands for the internal framework of a weld. This imaging capability is very useful for finding subsurface defects such as porosity, incorporations, and splits that might not show up with surface area examinations.
The process includes positioning a radiation resource on one side of the weld and a detector on the contrary side. Variations in material thickness and thickness affect the depletion of the rays, creating a contrasting photo that exactly defines flaws. RT is particularly beneficial for examining intricate geometries and thick areas where other approaches may fail.
In spite of its effectiveness, radiographic evaluation has to be conducted with stringent adherence to safety and security methods as a result of the dangerous nature of ionizing radiation. The interpretation of radiographs needs experienced workers, as the top quality of the analysis straight affects the reliability of the assessment. Continuous advancements in electronic radiography are boosting photo quality and interpretation efficiency, strengthening RT's vital duty in making sure weld top quality.
Laser Scanning Developments
Accepting laser scanning innovation in welding evaluation has transformed the assessment of weld top quality and honesty. Unlike standard examination strategies, laser scanning supplies rapid information acquisition, significantly enhancing the efficiency and accuracy of weld analyses.
Laser scanning developments have actually brought about significant enhancements in characterizing and finding surface area flaws such as porosity, lack of blend, and damages. The high-resolution data allows inspectors to perform extensive evaluations, making sure that welds fulfill rigid industry requirements. This method sustains the development of digital records, facilitating long-term high quality assurance and traceability.
Additionally, laser scanning modern technology integrates flawlessly with software program solutions created for automated flaw discovery and assessment. my company The resultant data can be easily shared and examined, promoting joint decision-making processes. As industries continue to demand higher requirements for weld top quality, laser scanning continues to be at the forefront, offering unparalleled accuracy and effectiveness in welding evaluation.
Automated Assessment Equipments

Automated examination systems supply the advantage of consistency, eliminating human error and subjectivity from the inspection procedure. They are made to operate in various environments, from manufacturing floors to remote field websites, ensuring thorough coverage. Welding Inspection Madison. These systems can be configured to stick to details welding criteria and requirements, giving comprehensive reports and documents for quality assurance objectives
Moreover, the combination of cloud-based platforms promotes the storage space and evaluation of large quantities of assessment data. This enables trend evaluation and anticipating maintenance, allowing suppliers to resolve potential concerns before they intensify. The adoption of computerized examination systems is a critical action towards boosting the reliability and effectiveness of welding processes in commercial applications.
Enhancing Safety and Performance
A considerable facet of improving safety and security and performance in welding examination hinges on the combination of ingenious modern technologies that simplify procedures and alleviate risks. The fostering of innovative non-destructive testing (NDT) approaches, such as ultrasonic screening, phased variety ultrasonic testing (PAUT), and radiographic testing, plays a crucial role in making sure structural honesty without compromising the safety and security of the workers entailed. These strategies permit for thorough examinations with minimal downtime, lowering potential risks related to typical approaches.
Additionally, the application of real-time information analytics and artificial intelligence formulas has actually transformed the way inspection data is translated. By using important site anticipating analytics, possible problems can be recognized before they materialize into critical failings, guaranteeing timely interventions and maintenance. This positive method dramatically enhances functional effectiveness and safety in welding processes.
In addition, remote examination innovations, including drones and robot spiders furnished with high-resolution electronic cameras, make it possible for examiners to evaluate hard-to-reach areas without revealing them to hazardous conditions. This not only enhances assessment precision however additionally lessens human threat. By leveraging these advanced tools and methods, markets can achieve greater security criteria and operational performance, ultimately causing more lasting and reputable welding examination practices.
Verdict
The combination of advanced devices and techniques in welding assessment dramatically improves issue detection and makes certain architectural integrity. These improvements not just enhance examination efficiency however also contribute to boosted safety and quality assurance in industrial welding applications.

Ultrasonic screening developments frequently stand for the center of improvements in welding examination innovations.While ultrasonic screening technologies have established a high requirement in non-destructive exam, radiographic examination methods continue to play an essential duty in welding examination by supplying one-of-a-kind understandings right into material stability.Embracing laser scanning innovation in welding inspection has actually reinvented the evaluation of weld quality and integrity. As sectors proceed to demand greater requirements for weld top quality, laser scanning stays at the leading edge, using exceptional accuracy and efficiency in welding assessment.
Automated evaluation systems provide the benefit of consistency, removing human mistake and subjectivity from the look at here inspection procedure.